Moving Ground Plane
ACE's Moving Ground Plane - Unique in the World
ACE has enhanced its research and development capability by adding a seven-metre single belt Moving Ground Plane (MGP). ACE’s MGP brings new opportunities for testing to our existing clients and - for potential new clients - the opportunity to test in a world class facility with a team that is dedicated to providing solutions to your testing needs.
The MGP will give both motorsports and original equipment manufacturers the tools they need to:
- conduct research in a high-tech environment
- help companies and researchers create new energy-efficient products
- develop new technologies in areas such as active aero
- maximize energy efficiency
- reduce carbon emissions.
ACE’s MGP has a unique feature - a 'Plug-and-Play' swap between a dynamometer and the MGP, making ACE truly a “CAWT” – a Climatic Aerodynamic Wind Tunnel. Ours is the only wind tunnel in the world to share the same air flow for both full powertrain and thermal development on a dyno and world class aerodynamic force measurement using a MGP.
Specifications of the Moving Ground Plane
Specifications of the Moving Ground Plane
Wind Speeds
- Up to 130 mph, 210 km/h or 58.3 m/s
- Wind on yaw capability of +- 30o
- 13m2 nozzle (4.5m x 2.889m)
- Secondary Collector added for enhanced axial static pressure gradient and reduced pulsation at high wind speeds
- Vehicle laser alignment
Belt Length
- Belt is 2.3m wide and 7m long
- Track Width 46.4” – 66.8” (1178.56mm - 1696.72mm)
- Wheel Base 95.8” – 126.3” (2433.32mm - 3208.02mm)
Temperature
Temperature and humidity controlled airstream to maintain ambient testing conditions for increased sensor stability.
Roll-in Ready
For planning and lead time, it is expected that vehicles be in “Roll-In-Ready” condition. Vehicles should be available the day before the testing.
ACE uses a single belt wheel hub vehicle force measurement and restraint system. It is critical that ACE have enough lead time to ensure that wheel hub adapters are fabricated and ready in advance of the test property showing up. As well, depending on the vehicle and complexity, ACE will have a garage bay available to prepare the vehicle for testing.
Two Options to prepare for testing:
Level 1 | Static Ride Height | Dedicated Garage Access 1 Day Before Test |
Level 2 | Dynamic Ride Height | 2 Days Dedicated Garage Access |
If the test vehicle is not Roll-In-Ready, more lead time will be required and there may be preparation charges.
Honeycomb
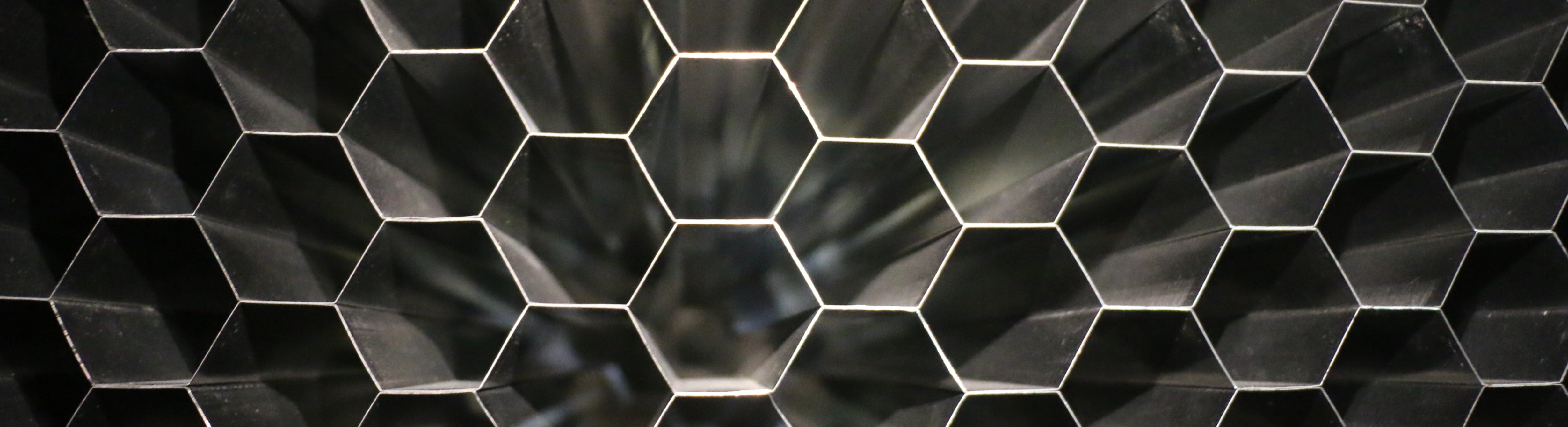
Secondary Boundary Layer System with Reinjection
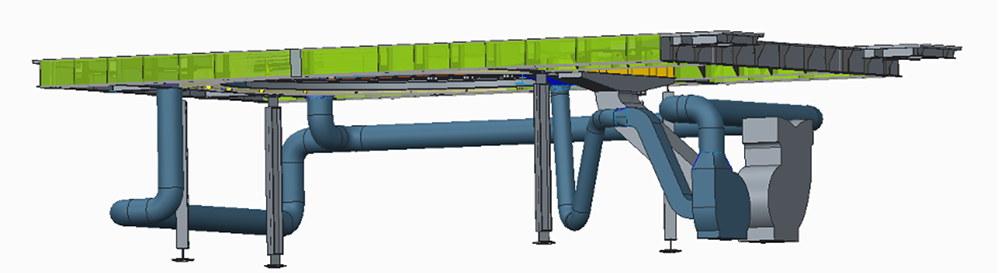
Primary Collector
The nozzle exit angle and collector adjustability work together to reduce the axial static pressure gradient (ASPG). This phenomenon is important for producing accurate drag on a vehicle as well as flow related to wake structures, which include cooling flow to the rear brakes and under-body. Users of aerodynamic wind tunnels require minimal ASPG to improve fidelity between wind tunnel and on-road flow conditions. The collector placed at the downstream end of the test section acts to control the axial static pressure gradient in the rear portion of the jet. Typically, the diffusion of the collector is adjustable, and this produces an effect significantly upstream of the collector.
Acoustic Panels
The Climatic Wind Tunnel was designed from inception with acoustic performance in mind and has always contained significant regions of noise attenuation within the airline circuit. These include acoustically treated transitions and annular silencers upstream and downstream of the main fan. Three of the four sets of turning vanes are also acoustically treated. These treatments result in significant attenuation of the mid and high-frequency fan-generated noise. The recently installed acoustic panels have reduced the background noise levels in the test section plenum. The acoustic panels cover the test section side walls, ceiling, rear wall and portions of the front wall and nozzle structure.
Frequently asked questions
-
Why is a Moving Ground Plane important to vehicle development?
Aerodynamic design has become more and more important in the development of modern road and race vehicles. Therefore, in wind tunnel testing, it is necessary to reproduce the natural conditions on a vehicle as precisely as possible. This is especially important now during the development of electric vehicles to maximize energy output.
-
ACE has a Burke Porter dyno in the Climatic Wind Tunnel. Is the Moving Ground Plane interchangeable with the Chassis Dyno?
Yes, the system is a 'Plug-and-Play' swap between a dynamometer and the Moving Ground Plane (MGP). We are the only wind tunnel in the world to share the same air flow for both full powertrain/HVAC development on a dyno and world class aerodynamic force measurement using a MGP.
-
How much lead time do I need to book the MGP?
We suggest contacting ACE as early as possible to book the CAWT several months would be ideal.
-
Once booked, how soon should I arrange for Roll in Ready preparation?
At least 6-8 weeks ahead of booked test date to facilitate vehicle prep.
-
How do I know my vehicle will be securely managed at ACE?
ACE has a robust security procedure for all of our customers. In fact, ACE is Controlled Goods Certified – authorized to conduct Defence testing so our security systems are of the highest standard.
-
Can we bring a full team of Engineers and Technicians to ACE?
Yes. ACE can accommodate your full team at our Facility. We have worked with large test teams from around the world including Europe, Asia and USA. Borders and test team size are not an issue.